


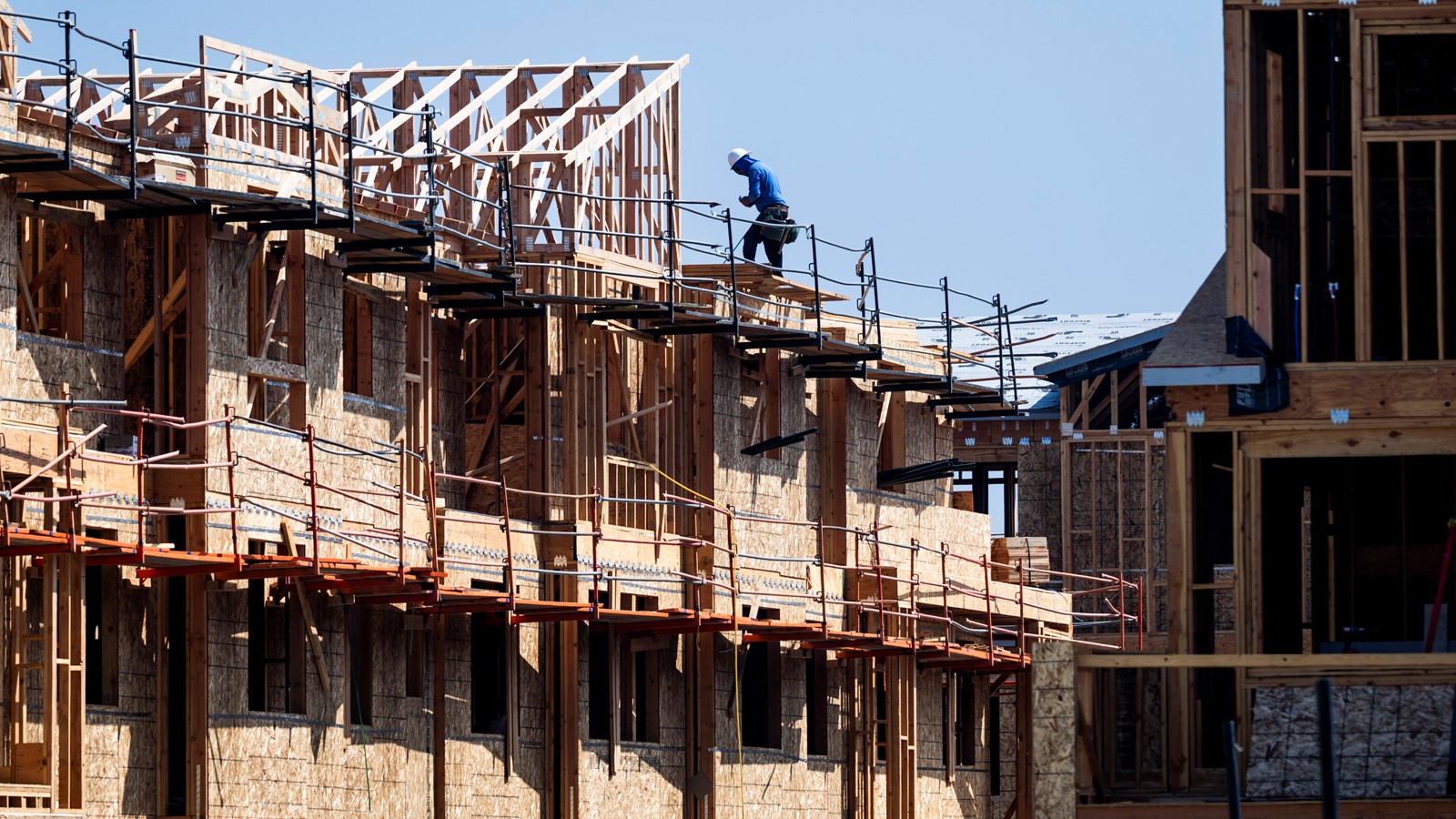
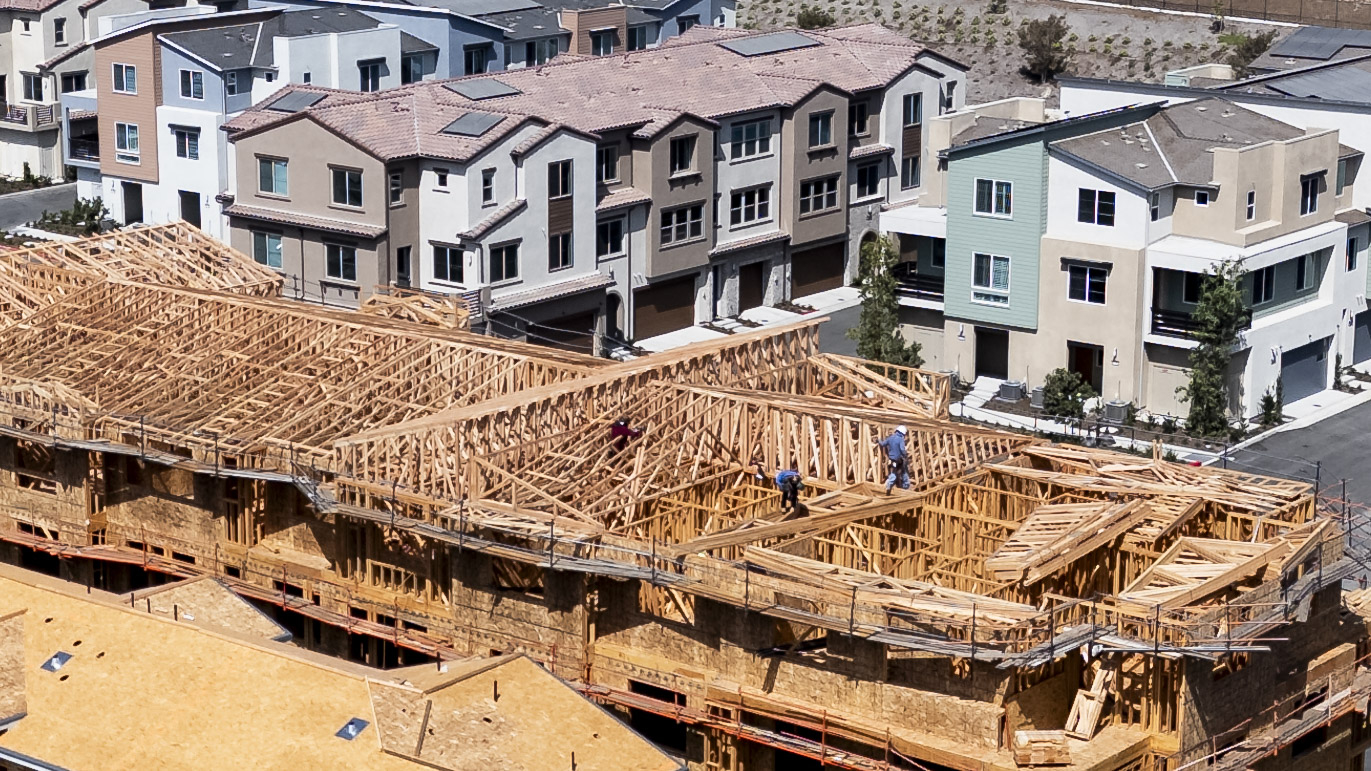
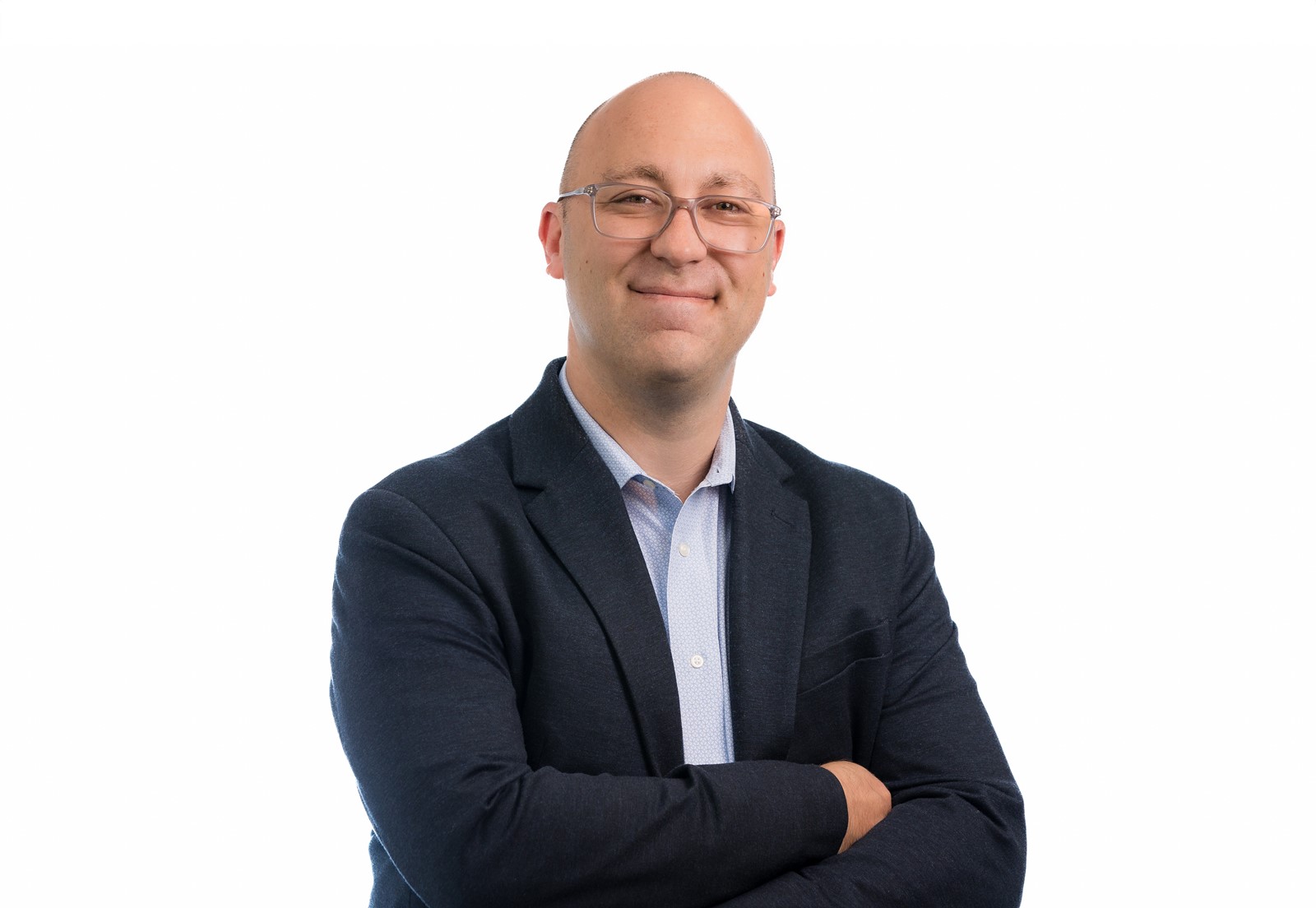
With a monthlong suspension of tariffs on Canada and Mexico expected to lift this week by President Donald Trump, the construction industry is bracing for higher prices on building materials and a supply chain shake-up.
The Trump administration’s new trade policies will likely drive up construction and labor costs in California and the U.S., a Zonda homebuilding adviser says. Everything from lumber needed for trusses in homes and drywall will cost more.
Underscoring the concerns for the industry, confidence among U.S. homebuilders in February dropped to its lowest in five months as high interest rates continued and concerns grew over Trump’s tariff proposals.
Todd Tomalak, a Newport Beach-based building products adviser with Zonda Home, sees challenges ahead for residential repair and remodel spending, a market he predicts will generate $1 trillion a year in revenue.
Companies that compete in this market range from Wisconsin-based Kohler Co., which makes plumbing, kitchen and bath faucets, to Illinois-based US LBM, which runs a network of lumberyards, distribution centers, kitchen and bath showrooms, hardware stores and truss manufacturing plants.
Tomalak expects the U.S. economy will slow this year as the country absorbs the impact of the tariffs, and deals with new worries over inflation, higher pricing on building materials and labor shortages.
“It’s a tough time to have a price hike,” he said of the tariffs.
Still, Trump said on Monday that tariffs aimed at Canada and Mexico would move forward early this month.
Tomalak cited statistics from the National Association of Home Builders showing residential construction already has absorbed 30% price increases in building materials since the beginning of the pandemic.
With new tariffs, U.S. building products could add an extra $29,000 in construction costs for a new home, according to the NAHB.
We asked Tomalak to share his thoughts about potential impacts of proposed tariffs, including rising costs and supply chain readjustments. His answers have been edited for clarity and length.
Q: What is your biggest concern, should the Trump administration impose the tariffs?
A: The housing industry should expect between 6% to 14% higher costs. Not all of that is directly due to the tariff, but we think that’s the number that they should be planning for, because there’s several other indirect effects that are likely to play out.
There are indirect price increases that we’ve seen in the industry in prior rounds of tariffs.
The quick version is that it is really hard time to try to pass along price increases. Excess savings are exhausted from the pandemic. That was true since about midsummer (2024); mortgage rates are higher, and we’re beginning to see a kind of overall fatigue with certain kinds of durable goods categories.
Q: What are the product categories where you’d expect price increases?
A: The category that is No. 1 in terms of getting hurt the most is lumber and plywood. It has direct exposure to tariffs imposed on Canada. There’s not much margin there. It’s a fairly straightforward commodity that gets hit.
So lumber, plywood and then you start getting into the hardware categories. Think window and door hardware components, then aluminum appliances. Those could all see cost increases above 8%.
The ones that will be less impacted are shingles, wallboard, stone, cement and things like that, which just don’t have the same amount of import exposure.
Q: Will the building industry look for alternative suppliers?
A: Yes. We saw this happen immediately after COVID. It took about two years or so for new lumber capacity to come back online. There’s a lot of Southern Yellow Pine lumber usage — or softwood — in construction. (Softwood lumber comes from an evergreen tree that produces needles and cones.)
There’s been no production increase in the U.S., but European imports may get a boost from the tariffs. But it all takes time. What people forget is readjustment is expensive and risky.
What I think suppliers worry about is that the tariffs are here today as a political tool and then get removed tomorrow, and their cost structure has changed so that they’re now in a tough spot. They’re going to be looking for indications of this being a long-term policy, not a kind of short-term bargaining chip.
Q: Does this mean deferred home sales, remodels?
A: Yeah. These things tend to fester but not go away. So what we’re seeing in the data is — and this is true ever since rates jumped up in 2022 — evidence of a deferred backlog of future home sales and deferred home improvement and remodeling projects.
If deferrals fall to historic norms, it has to jump up a lot — like multi-year, double-digit growth. That’s not our forecast this year.
We have a very cautious forecast this year, but I do believe that eventually you have to either improve your home, or you have to be willing to live in a dilapidated home.
Q: How long will tariffs hold back spending on remodeling projects?
A: We think that it’s going to be a rough six months for new construction, and for building materials.
We’re hoping that the deferrals begin to thaw around midyear in 2025 — but time will tell.
Q: How will all of this affect rebuilding after the Los Angeles fires?
A: With the L.A. (County) fires, you’re looking at about 16,000 structures (destroyed or damaged).
The tariffs do make the costs hard. It makes the rebuilding more challenging. But our sense is the biggest challenge is going to be on the labor side.
You could see hourly wages increase by $9 an hour on top of what they are right now.