


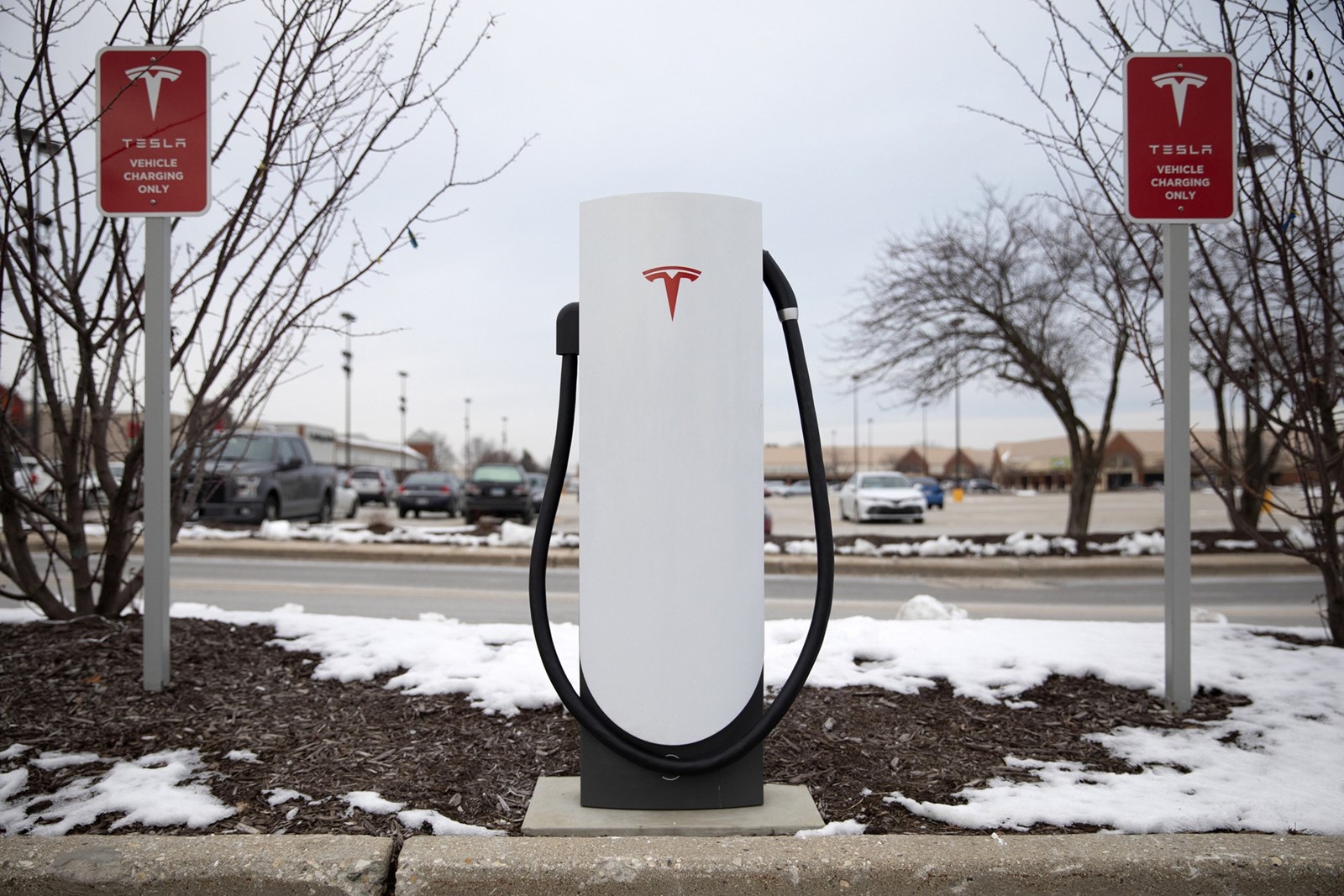
Skeleton Technologies Group OU is working on supercapacitors, lightweight and long-life components that can distribute intensive bursts of power. These may help eliminate lead-acid batteries, a piece of technology invented in 1859 that still lurks under the hoods of Teslas in addition to the main lithium-ion power source.
Supercapacitors have some way to go before they are widely adopted.
There is still a gap with the popular lithium-ion units on how much energy they can store, Skeleton Chief Executive Taavi Madiberk said.
Even so, the technology is promising for offering higher peak power output and reliability in extreme temperatures, and Skeleton has already sold it to clients across the transport industry.
“Sometimes people think that lead is a problem of the past because it relates to internal combustion engines but in practice all electric vehicles have 12-volt lead acid batteries,” Madiberk said. “We are working on a viable alternative to replace all lead acid batteries.”
Tesla Inc. Chief Executive Elon Musk moved to Silicon Valley in the first place to do research on supercapacitors in his doctoral studies at Stanford University, he wrote in a blog post in 2006. While Musk eventually dropped out from Stanford to start his new ventures, he hasn’t abandoned his bet on supercapacitors, also referred to as ultracapacitors.
Tesla, also searching for a breakthrough for electric car batteries, bought Skeleton’s competitor Maxwell Technologies Inc. last year. Musk’s company, like other manufacturers, still uses the relatively cheap and recyclable lead-acid battery in addition to the lithium-ion unit.
The sector is at a stage where the lithium-ion battery industry was around 1999, according to Madiberk, whose company also has a base in Germany. Back then, lithium-ion batteries cost over $5,000 per kilowatt-hour, compared with under $200 now. Supercapacitors may similarly go from $5,000 to as low as $300, he said, without giving an exact timeline.
The technology may be useful for some tasks such as regenerating energy from braking, perhaps in conjunction with a lithium-ion unit, said James Frith, an analyst at BloombergNEF who focuses on energy storage. However, it’s only one of a number of available routes for the industry.
“There’s been a lot of interest in supercapacitors over the years,” Frith said. “The trouble is that lithium-ion batteries have been coming down in price quite rapidly.”
To replace lead-acid batteries, Skeleton is cooperating with some major European carmakers, Madiberk said, without disclosing names.
Its products reach an energy density — a key measure of performance — of 60 watt-hours per kilogram, exceeding regular lead-acid batteries. Their raw material, a patented graphene composite, provides cost advantages in the long term not just compared with lead-acid but also lithium-ion batteries, he said.
“If you look at the supplies of cobalt, lithium, nickel, manganese, then sooner or later with electrification we see significant bottlenecks,” Madiberk said. “The issue with lead is, of course, it’s toxic: the manufacturing process is environmentally harmful.”
In heavy transportation, Skeleton has supplied systems that recuperate the braking energy of trams made by Czech manufacturer Skoda Transportation AS and that reduce the fuel consumption of hybrid-electric buses made by the U.K.’s Wrights Group Ltd.
Aside from Tesla, Madiberk lists U.S.-based AVX Corp. and China State Railway Group as key competitors. The raw materials Skeleton uses have given it a competitive advantage over bigger rivals, he said.