


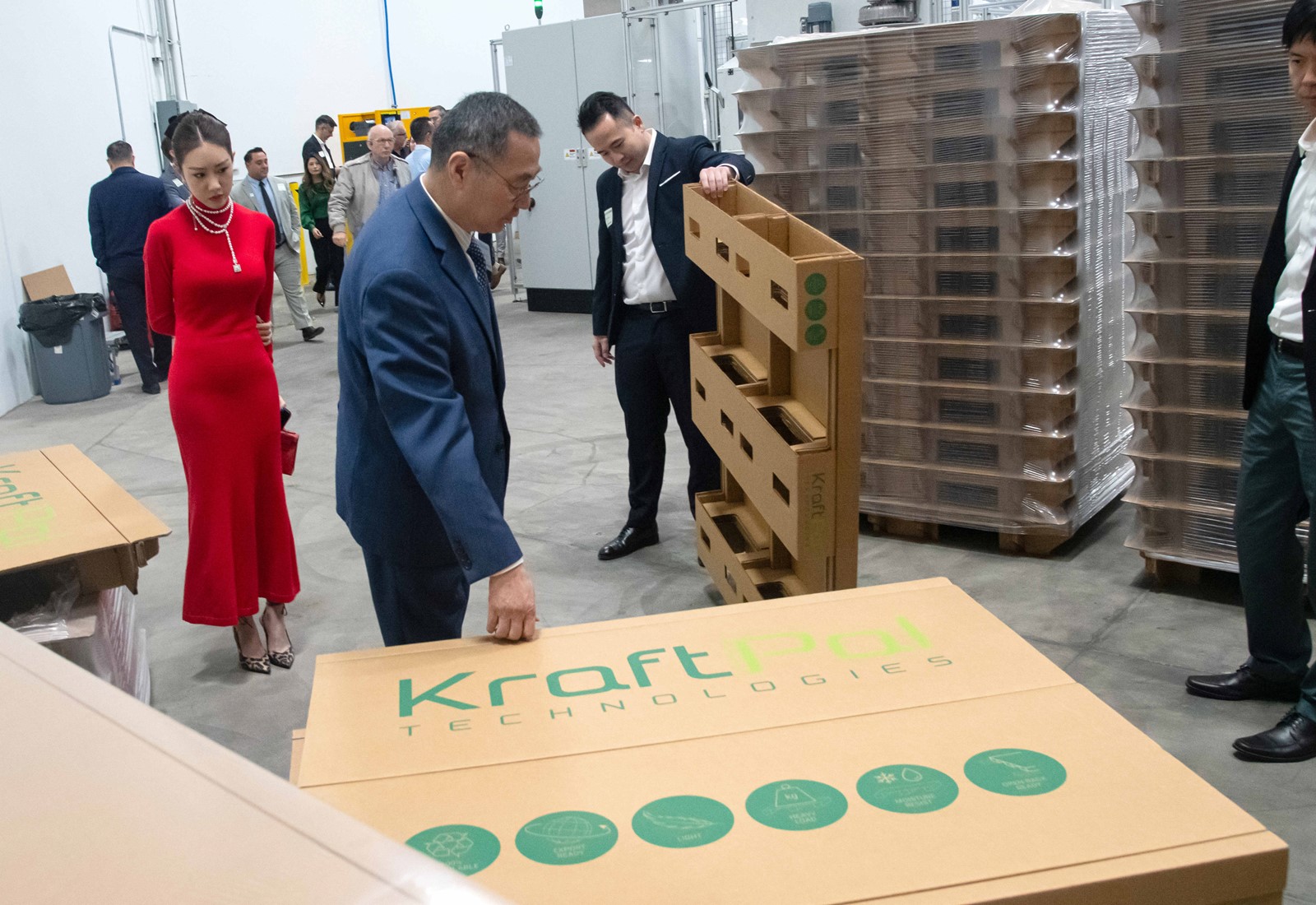
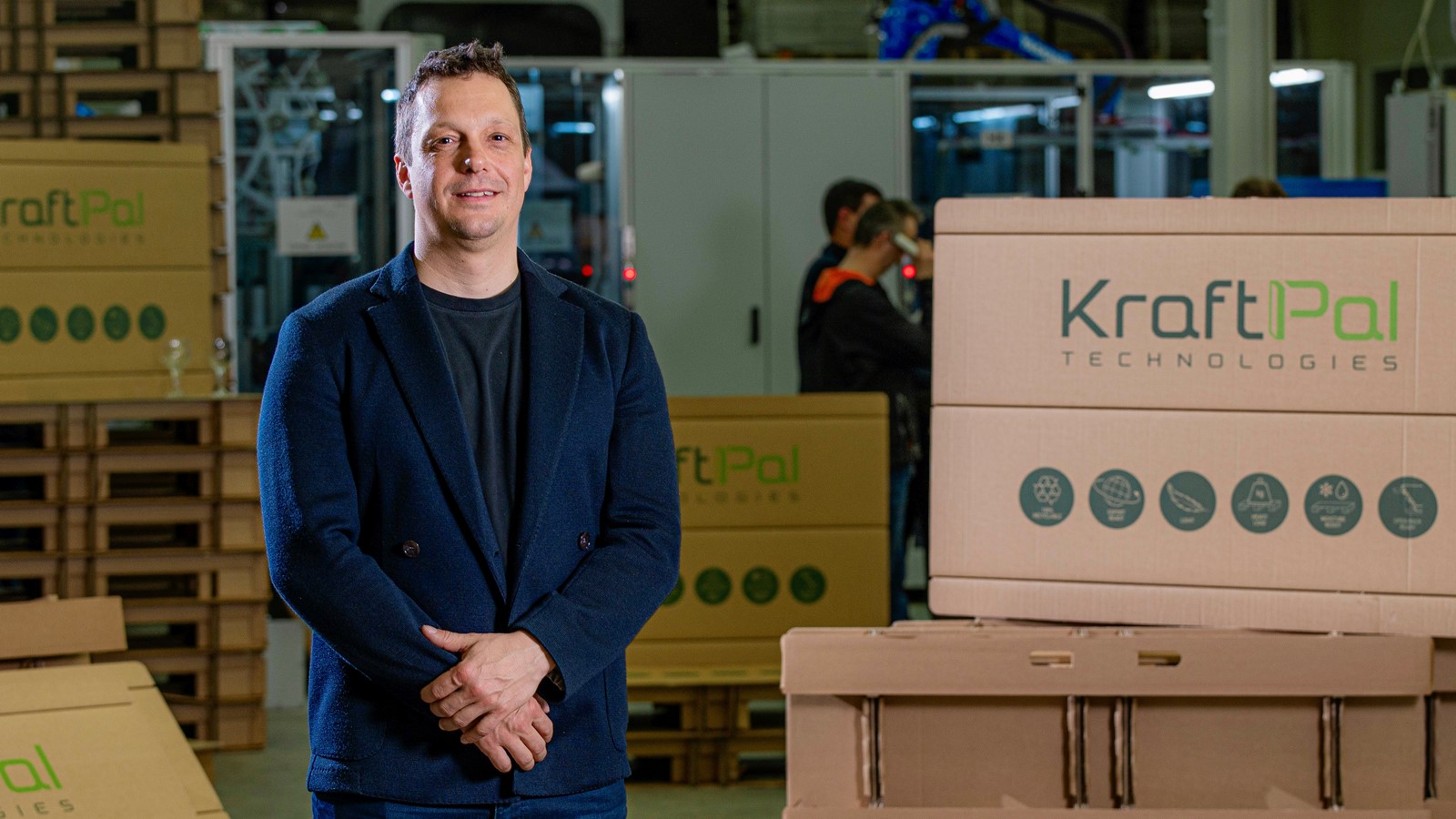
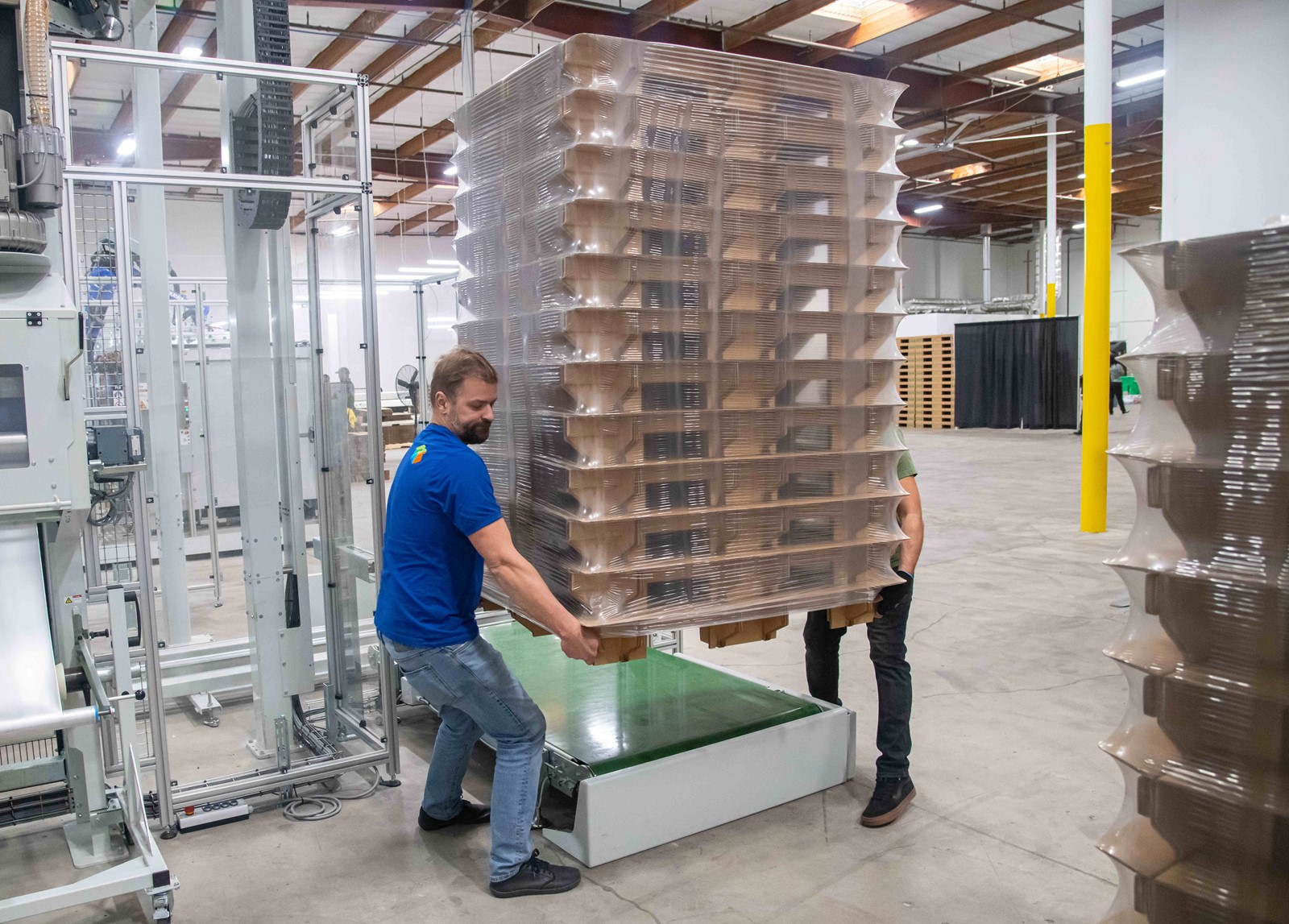
Former professional skier Gregor Brajovic knows what it feels like to overcome hardships.
The Slovenian-born entrepreneur was about to compete in the Winter Olympics in Turin, Italy, in 2006 when he had a career-ending crash at 70 mph in the Swiss Alps.
While the accident ended his chances of competing on the world stage, the determination he showed in recovery became one of his hallmark traits in getting his business, KraftPal Technologies, off the ground.
“In skiing, you take so much risk all the time. It’s not some sport where you just twist your ankle or something. When you crash, you get hurt. I’ve crashed many times, but I always jump back in,” said Brajovic, who adopted the same work ethic when KraftPal’s mission to manufacture corrugated cardboard pallets nearly failed.
“We tried out the first generation of our technology to make pallets in Slovenia, and we completely failed,” said Brajovic of their initial efforts in 2011. “We sat around looking at each other, went home, came back the next day and restarted the project, which is when we came up with our interlocking system to strengthen the crates.”
That was the birth of today’s KraftPal, a London-based startup pallet maker founded by Brajovic, its chief executive.
This month, Brajovic opened a 32,000-square-foot corrugated cardboard pallet factory in Southern California, the first for his company in North America. The company also has factories in Austria, Finland and Saudi Arabia.
Brajovic’s proprietary system for KraftPal involves a robot-driven process of bending, folding and gluing together sheets of mostly recycled, corrugated cardboard. The goal is to design a pallet that can handle varying weights of freight and shifting loads, ranging from shoeboxes to machine tools, and then be recycled to a customer’s specifications.
Over the years, Brajovic has tweaked the technology behind the Palletonator, a machine roughly the size of a 2,500-square-foot home that produces about 600 pallets per hour.
A wooden pallet weighs about 60 pounds, and KraftPal’s cardboard pallets are just under 15 pounds and can withstand up to 4 tons of weight and absorb vibration. The lighter weight pallet also helps cut down freight costs.We asked Brajovic about how he has positioned his company for growth. His answers have been edited for clarity and length.
Q How did you go from alpine skier to making cardboard pallets for KraftPal?
A I was looking for disrupting technologies. I stumbled on a novel project that originally became popular after World War II.
Everyone knew that we needed a cardboard pallet because they are fully recyclable, but nobody ever tried to develop a pallet that would perform well enough that the market would accept it.
Q Are cardboard pallets less expensive than wooden ones?
A Compared to wooden pallets sold here in California, and the size and type of cardboard pallet you buy, the ones we sell can cost slightly below the cost of wooden ones. They are selling at a price for the benefits they bring. If you are moving cargo via air freight, every 1 kilo (2.2 pounds) would cost you $2, and if you are moving cargo that is 20 kilos lighter, it’s like $40 in savings on just that shipment.
The shippers also receive carbon emission credits that lower the costs of the pallets in their bookkeeping, the corrugated cardboard is fully recyclable, and the pallets are clean and don’t have the hygienic issues of wooden crates. Once you send it out, the end user can recycle it and get the cash back.
Q Are there any competitors?
A There are some competing in different markets, but we are really competing against wooden pallet manufacturers. Some competitors have pallets offered for rent. Our market is one-way, with long-distance shipments only. With our pallets, you’re shipping something to Europe, or to China, or across the U.S., and it’s never coming back.
Q How has private equity firm Pasaca Capital of Pasadena helped with your company’s growth?
A It has helped with research and development, and positioned us with adding two more pilot plants. The $124 million investment was just a commitment. We have not taken it all. We received less. R&D is in Slovenia, but there is a design center here in Ontario where we can handle minor developments or drawings for our clients for specific items.
Dr. Charles Huang, who is the founder and CEO of Pasaca Capital, invested in us because of our environmentally friendly manufacturing, the disruption we can bring to the pallet market and the exit strategies that are available through an IPO.
Q What makes the Palletonator unique?
A No. 1, I can produce designs that are unique, and produce a corrugated cardboard product that can hold very heavy things. The Palletonator does not cut the corrugated cardboard. We get precut sheets that we feed into the machine and the final product comes out.
There’s no cutting in our production, only folding, creasing, gluing and assembling.
Q What are some of the pitfalls that your business has encountered?
A The pitfalls can be the people. You need to be careful with who you hire when you grow. Our successes are based on a few core people who have shouldered a lot of the responsibilities.
We’d rather grow slower and do the proper training and testing with people than go faster. So many of our key people are from the sports world. It’s almost easier in business and life than in sports.