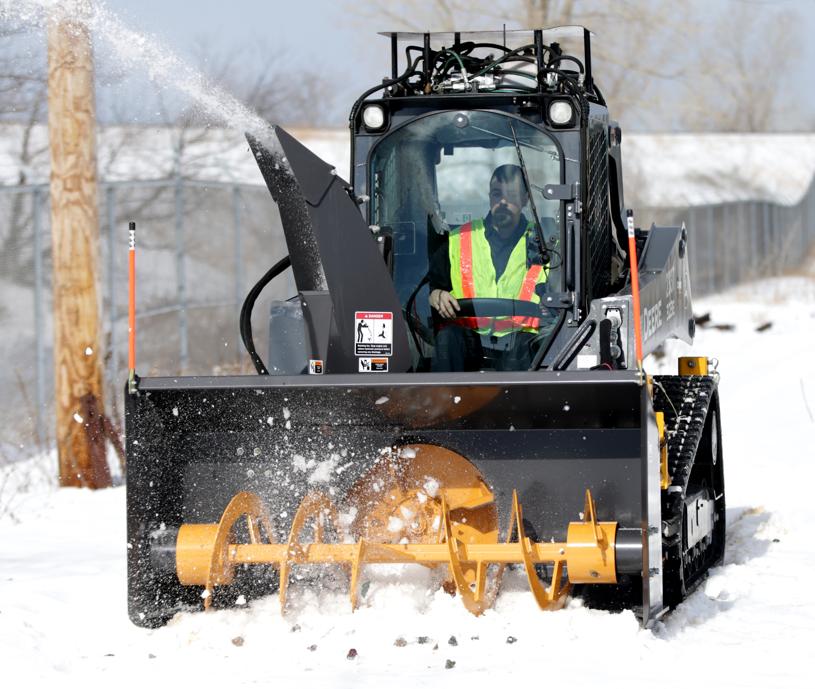
They say necessity is the mother of invention. But Michael Haywood was driven by plain embarrassment.
The nightmarish winter of 2015 was at its worst, a barrage of powerful storms that brought the MBTA to its knees. In desperation, state officials called in prisoners and the National Guard to help the transit system dig out, one shovelful at a time.
For Haywood, an MBTA machinist who fixes snow-clearing equipment, it was a personal affront. There had to be a better way, he thought.
So he thought of one: mounting a John Deere vehicle often used to scoop dirt — it’s called a skid-steer loader — onto railcar wheels in order to clear the snow-packed tracks. It sounded farfetched, and some of his colleagues were skeptical.
But Haywood and his colleagues kept welding. Over 12 hours, they assembled a new kind of snow blowing machine, bringing Haywood’s vision to life. To the surprise of his naysayers, the contraptionworked.
Two years later, the MBTA has hired a company to build eight machines based on Haywood’s prototype, a small fleet than can clear miles of track far faster — and more cheaply —than before. In just a couple of hours, the rolling snow blowers can clear areas that under one old method, a jet-fueled melting machine, would have taken nearly a day, and with far greater precision.
“It’s like using a scalpel versus a hatchet,’’ Haywood said.
Haywood, a 35-year-old known to his co-workers as “Haywire,’’ became a machinist because he “doesn’t like to not know how to do things.’’ He started out at the MBTA repairing buses, then joined a crew assigned to fix utility vehicles, basically anything that didn’t carry passengers.
Working alongside 25 other machinists in a Charlestown garage, the Billerica native found a like-minded boss in superintendent Bill Walsh, who grew up in Weymouth and joined the MBTA nearly 25 years ago.
Walsh knew to pack a bag of extra clothes and food when bad snowstorms approached. While his employees caught a few hours of sleep on a couch or armchair in the breakroom, Walsh was often wide awake, planning out the next day.
In 2015, Haywood had been living out of his luggage in the garage for three weeks, working 20-hour days and watching in dismay as the MBTA’s performance came under heavy criticism. One day, as Haywood was about to head home to pick up fresh clothes, Walsh made a personal appeal, urging the crew to “think outside of the box’’ to help the system recover faster.
Crews had been running trains on the tracks to clear the snow, but it wasn’t enough. On some lines, the best snow-clearing devices hadn’t been put out quickly enough, while others had fallen into disrepair. Workers were running out of places to put all the snow, and dealing with a bitter cold that kept it frozen and packed.
“It kept snowing and snowing and snowing, and we had to come up with something,’’ Haywood recalled.
As he drove home to Billerica, he took a mental inventory of the machines he fixed every day, searching for an answer. Finally, it clicked.
The next day, he rushed to the mezzanine of the MBTA’s hulking garage on Arlington Avenue, grabbing a pair of spare rail wheels they had salvaged from a vehicle bound for the junk yard. He quickly started welding the wheels onto a skid-steer loader, which was outfitted with a snow blowing attachment. With the right adjustments, he hoped, the plow would be able to move fast enough to blow away heavy snow and ice.
Walsh thought the idea had promise. Others had doubts.
“We had people who said, ‘That’s not going to work; you’re wasting your time,’ ’’ Walsh said. “They just weren’t buying into this.’’
The pessimism ran counter to the crew’s work ethic. Haywood likens Walsh to New England Patriots coach Bill Belichick in his high expectations and no-nonsense approach. Failure isn’t an option, he would tell his crew. There is no “can’t.’’
For Haywood, who thinks of his job as “figuring out nuts and bolts,’’ the skepticism only deepened his resolve. On Feb. 15, 2015,a bitterly cold day that followed another major storm, he and another worker dragged their invention to the Mattapan trolley line.
The 2.5-mile Mattapan line is typically closed during big storms, since the 70-year-old vehicles can’t withstand the snow as well as newer vehicles. By the time Haywood got there, the rail was covered in about 8 inches of packed snow, flanked by 3-foot snowbanks.
But on its first trip, the juryrigged snow blower cut through the snow with ease, freeing the dark tracks that had been buried in white. Haywood and his co-worker were ecstatic, although they knew it needed adjustments.
By the following year, as Governor Charlie Baker touted an $80 million “winter resiliency plan’’ for the agency, MBTA officials had contacted Mitchell Rail Gear, a Michigan-based company, to customize the machine. For an agency trying to cut costs wherever it could, the $100,000 contraptions were far more attractive than traditional snow blowing machines.
Estel Lovitt, the owner of Mitchell Rail Gear, said he was immediately intrigued. His company already attached railcar wheels to MBTA vehicles such as maintenance trucks, which make their way down the tracks every night so workers can tend to problems big and small as the rest of the region sleeps.
“I think it was ingenious,’’ Lovitt said.
The company had to figure out how to put retractable wheels onto a track loader, and how to keep it from derailing when it hit a small bump or sharp turn. Lovitt figured out that a hydraulic suspension system would allow the wheels to raise and lower themselves so they kept in constant contact with the rail.
“You got all four wheels and they were all working independently to keep it in balance,’’ he said. “That was really the secret of making this thing work.’’
Lovitt has added the customized machine to its website, and a company from Canada has already ordered one. He thinks more will follow.
Even with Lovitt’s interest, Haywood and Walsh still faced some doubts. At one point, the MBTA had to wait for John Deere to make sure the retrofits wouldn’t void the machines’ warranty.
When a John Deere official came to inspect the prototype, he was impressed enough to give his blessing. Haywood said he asked where he had gone to engineering school (he hadn’t) and whether he might want a job with the company.
But Haywood says he doesn’t want to leave the MBTA, with its frenetic pace and myriad challenges, anytime soon. Walsh, who each winter tells Haywood it’s his last, doesn’t seem to be going anywhere, either.
Especially with the new device making winters a little more manageable, Walsh said.
“I don’t think you’ll ever see the MBTA shutting down again,’’ he said.
Nicole Dungca can be reached at nicole.dungca@globe.com. Follow her on Twitter @ndungca.