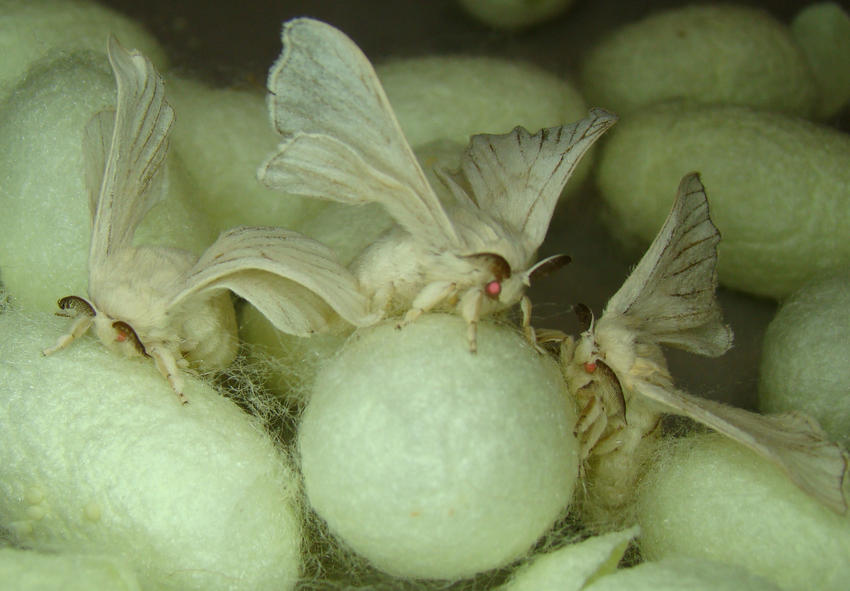
Silk is an elegant material, often used to manufacture delicate garments like camisoles and scarfs. It’s also incredibly tough, good for catching flies or stopping bullets. Wait, what?
A startup company is trying to do what others before (yes, it has been tired) have failed to achieve — harvest spider silk in order to create body armor for the military.
The company, Kraig Biocraft of Ann Arbor, Mich., recently signed a contract with the Department of Defense to manufacture “ballistic shoot packs,’’ which will be used in preliminary firing-range tests. If those go well, the company will receive additional money to improve its spider silk and — one day — manufacture ballistic garments. It’s basic military procurement, except in this case the underlying material is completely novel: a spider-inspired product called Dragon Silk that is tougher than Kevlar because it’s able to stretch without breaking.
Kevlar is notoriously brittle. “It breaks at 3 percent stretching,’’ says Jon Rice, chief operating office at Kraig Biocraft. “Spider silks can stretch 30 to 40 percent, and, because toughness is [a combination of] elasticity and strength, spider silk is tougher than Kevlar.’’
Silk has a long history of military applications. Chinese and Japanese warriors donned protective silk garments more than a millennium ago. Archduke Franz Ferdinand of Austria owned a bulletproof silk vest, too. Unfortunately, he left it at home on June 28, 1914. Tests conducted at the Royal Armouries in England in 2014 confirmed that the vest likely would have stopped the assassin’s bullet that killed him that day.
Spider silk is the strongest natural silk of all but also the hardest to harvest. While huge colonies of silk worms agreeably spin their silk cocoons in factory settings for harvesting, factory-farmed spiders attack one another. Over the years, researchers have tried different workarounds, including a project out of the University of Wyoming more than a decade ago to genetically engineer goats to produce spider silk proteins in their milk. That didn’t work because once the researchers had collected the proteins, they still had to spin them into silk threads — and the process they used kept producing a finished product that was brittle. To avoid that problem, Kraig Biocraft takes an even more direct approach, genetically modifying silk worms that produce the proteins and do the spinning.
“The silk worm is nature’s silk protein factory,’’ says Rice. “For thousands of years we’ve designed these guys to produce 50 percent of their body weight in silk protein. We have this great silk factory, [the question was], how do you change the recipe inside worms?’’
That work proceeded in two steps. In the 2000s, biologist Randy Lewis at the University of Wyoming (who’s now at Utah State University) identified the sequences of spider silk genes responsible for their remarkable strength and flexibility. Around that same time, geneticist Malcolm Fraser at the University of Notre Dame developed a tool called piggyBac for inserting novel genes into insect genomes. In 2006, Kim Thompson, founder of Kraig Biocraft, approached Fraser and asked him if it was possible to use piggyBac to introduce these spider silk genes into silk worms.
“He came to me and said he had these genes and would I be able to engineer them into a silk worm and make spider silk in the silk worm,’’ says Fraser. “I said, yeah, of course.’’
It’s taken some time. Over the last half-decade, Fraser and his colleagues, including biologist Don Jarvis at the University of Wyoming, have created increasingly powerful transgenic worms by injecting genes into worm eggs and breeding the top-performers. The product they’re trying to re-create is the silk made by the Golden Orb spider, specifically its dragline silk. Currently they’re able to closely approximate it. Soon, they hope to achieve the full trick, completely replacing the worm’s native silk with their own spider silk design. Other experts in the area consider the work promising, while noting that it still has a long way to go.
“It does seem like a good argument [Kraig Biocraft] put[s] forward, but it is still quite a small investment at this stage,’’ Gareth McKinley, an engineer at MIT who worked on the goat-spider silk project, writes in an e-mail.
For the military, the appeal is clear. As anyone who’s ever wrapped themselves in a high-end robe can attest, silk is light and breathable, and conforms lightly to the human body. That makes for a nice morning lounging in bed and also a better experience in a combat theater. The spider silk armor could be worn underneath hard ceramic plates to prevent bullets or shrapnel fragments from penetrating to lethal depths. It might also offer protection for parts of the body that are difficult to shield with rigid armor.
“One of the key methods of injury from [improvised explosive devices] is tiny little fragments that penetrate the groin, pelvic, and anal areas,’’ says Francisco Martinez, chief technology officer for the Boston-based company Protect the Force, which makes equipment for soldiers. “Those are areas where, when a fragment breaks an artery, it’s hard to stop the bleeding.’’
This new spider silk technology is still in early stages and may never make it to market. But it’s more certain that the kind of light, strong material you can make from spider silk is the future of body armor. And, while it may be odd to picture soldiers draped in silk, a certain comic book superhero long ago established that a skintight spider suit is good gear, if you can get it.
Kevin Hartnett is a writer in South Carolina. He can be reached at kshartnett18@gmail.com.